
The Plastic Injection Moulding process was developed
by David Wesley Hyatt in 1868, by using a plunger method. The technology
for this procedure has now progressed. Most manufacturing models make
use of heated barrels where the melted plastic is fed. It is combined
with plastic granules and compelled to form a mould cavity. Once this
happens, the moulded cavity is chilled and then solidified. The clamping
part of the machine, then goes on to mould the plastic into appropriate
shape. The professional can then design the mould and then the mold is
manufactured by the company in iron or aluminium to make appropriate
parts in precision machines.
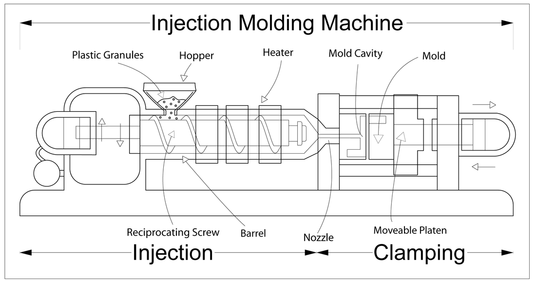
The procedure of custom plastic injection moulding
usually starts with a commercial designer or professional who design a
product. This is followed up by the work of a toolmaker or mould
manufacturer who makes the mould to fit the design created. These moulds
are metallic and usually designed using either steel or aluminium.
Using devices, they are designed to obtain the actual shape preferred by
the design. Once this is done, the procedure of actually making the
plastic follows. This includes polycarbonate and thermosetting plastic
content being fed into a warmed barrel and combined. This melted
material is then pressured into the cavity of a mould and there it cools
down and solidifies to form the desired part.
Like other commercial procedures, there are a variety
of aspects that should be managed to ensure that result is the best
possible, with as little pollution as possible. The injection speed can
be enhanced by varying the viscosity of the material. The greater the
viscosity, the greater the pressure loss and thus the lower the speed.
The greater the speed, the greater the shear rate and viscosity.
Although increasing mould and melt temperature ranges will reduce the
viscosity, thus improving pressure, it will also decrease the shear
rate. Also, the cooling time can be manipulated, the warmer the
dissolved plastic materials, the longer for the plastic materials to
cool and thus the thicker the item produced. The Gate Speed and Metering
Phase can also be adapted to generate the best possible results.

Please check out our website for more details on our services related to custom plastic injection moulding Brisbane.
No comments:
Post a Comment